一、【 客户物料及工况信息 】
项目 | 详情 |
---|
物料名称 | 活性炭粉末 |
包装规格 | 5kg / 包 |
粒径范围 | 5-10μm,粉末细腻易扬尘 |
堆积密度 | 0.3 - 0.4 g/cm³ |
环境要求 | 投料时常温常压,需适应反应釜 120℃高温及蒸汽环境 |
设备接口 | 反应釜进料口离地 3 米,口径 DN150 |
二、【 客户核心需求 】
产能需求:每小时输送 100kg 活性炭粉末,适配反应釜 DN150 进料口;
环保需求:全流程密闭输送,杜绝粉尘外溢;
品质管控:配置金属剔除装置,防止金属异物污染物料;
可视化监控:管道设置观察口,实时查看上料状态;
安全省力:利用自动化输送替代人工,降低操作风险;
其他要求:依托现有压缩空气源,无防爆需求,设备需稳定耐用。
三、【 核心设备选型及配置 】
配置 | 详情 |
---|
可视窗口 | 投料盖板配备带灯透明亚克力观察口,便于实时查看投料状态。 |
永磁棒过滤 | 投料口安装可拆套筒式永磁棒,有效吸附铁磁性杂质,确保物料无金属污染。 |
滤芯过滤 | 采用褶皱覆膜滤芯(过滤精度 0.3μm),高效捕集逃逸粉尘,过滤效率≥99.9%。 |
缓存仓设计 | 下方设 5mm×5mm 格栅(防大颗粒异物)及 130L 缓存仓,均衡物料输送节奏,减少频繁拆包。 |
功能 | 实现人工拆包投料的粉尘隔离与金属异物剔除,保障操作环境安全洁净。 |
配置 | 详情 |
---|
驱动方式 | 利用压缩空气驱动,通过真空吸附原理输送物料,适配 100kg/h 产能需求。 |
管道系统 | - 采用 SUS304 不锈钢管道(直径 51mm),耐腐蚀、易清洁; - 在高度 1.5 米处配可视窗口,实时监控物料流动状态。 |
阀门配置 | 管道与反应釜进料口通过快装结构连接隔温气动球阀,该球阀可耐受 120℃蒸汽环境,并与上料机联动:上料机启动时,球阀同步开启;上料机关闭后,球阀延迟 3-5 分钟自动关闭,确保管道内残留物料完全输送至反应釜。 |
滤芯配置 | 配置褶皱覆膜滤芯(0.3μm 过滤精度),防止粉尘外泄,确保排气洁净。 |
智能控制 | 单片机控制,可实时调整上料时间、下料时间、反吹时间,适配不同工况需求。 |
自动清管装置 | 管道系统配备自动清管装置,定期清理管道内壁残留物料,确保输送效率与稳定性。 |
四、【 方案示意图 】
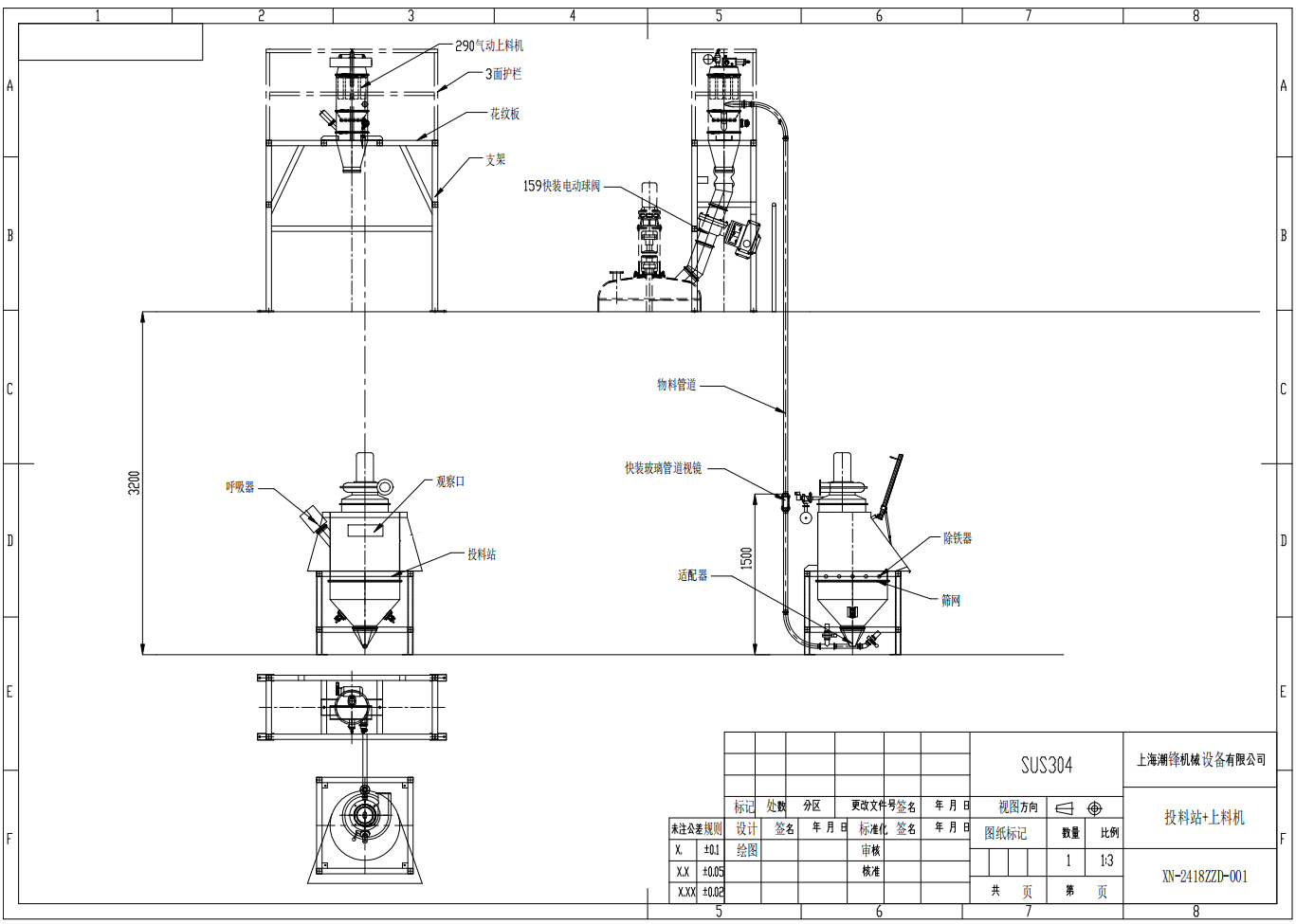
五、【现场图示 】
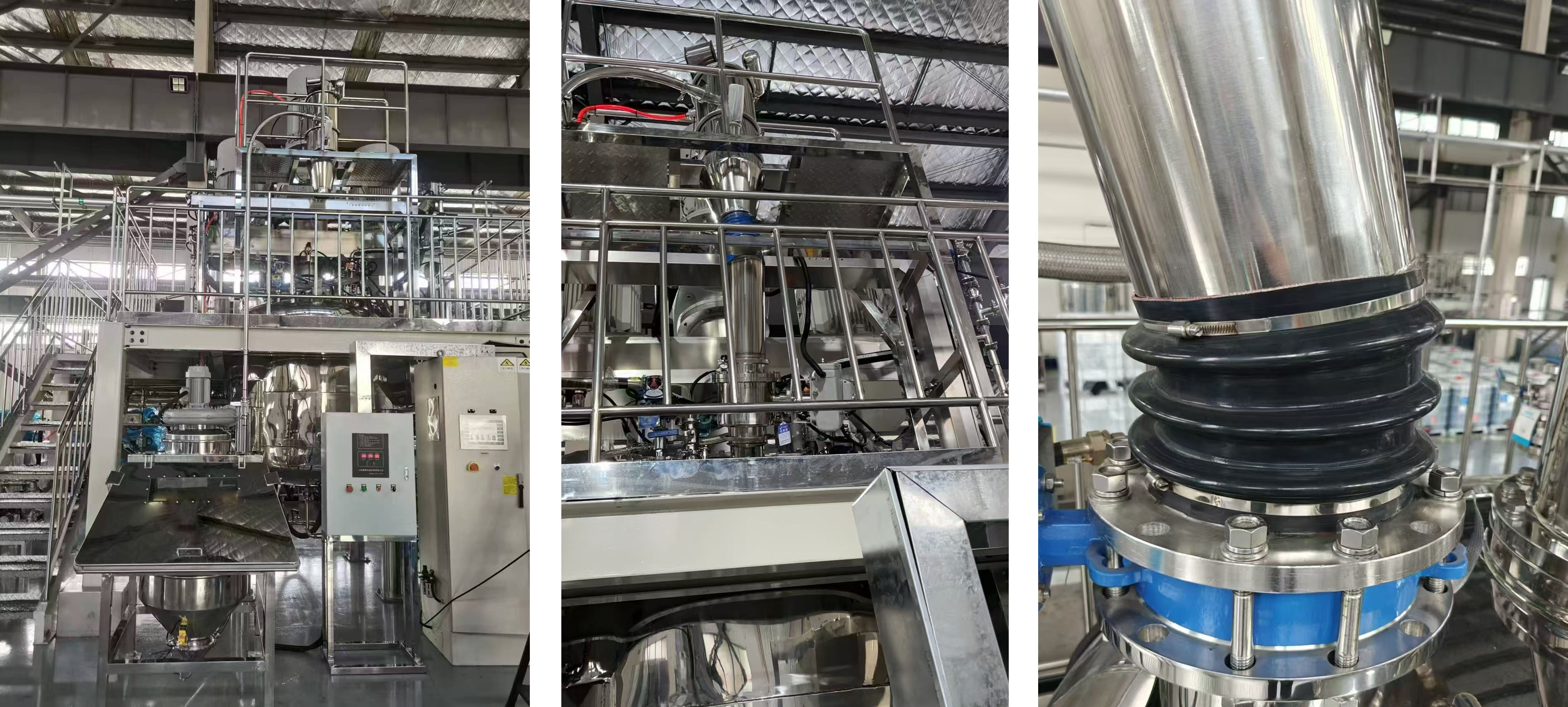
五、【 该案例的优势 】
粉尘零泄漏:
金属异物防控:
智能化联动控制:
操作便捷性:
气源需求:利用客户现有压缩空气(0.5-0.8MPa),耗气量约0.72m³/min。
温度耐受:SUS304 管道及隔温气动球阀可长期适应反应釜 120℃蒸汽环境,避免物料粘壁或设备老化。
维护成本:滤芯支持在线反吹清洁,更换周期≥6 个月;永磁棒可拆洗重复使用,年维护成本≤2000 元。
总结:该案例通过 “无尘投料 + 气动输送 + 智能控制” 三位一体设计,彻底解决客户人工投料的粉尘污染与劳动强度问题,同时满足新能源材料行业对异物防控与流程可视化的高要求,实现安全、高效、洁净生产。